В философии нашего бренда всегда лежала приверженность высокому качеству. На протяжении многих лет это было и остается одной из главных ценностей для команды создателей NIKOMAX.
Иногда, простите за игру слов, это достигается ценой не самой низкой цены относительно «соседей по рынку». Мы в Тайле уже давно приняли этот постулат как данность и, не удивляйтесь, не так часто выпячиваем его для внешней аудитории. У нас не самый агрессивный маркетинг среди конкурентов и даже не самый «навороченный» сайт. Зато все сотрудники отделов продаж знают – у NIKOMAX самое лучшее качество среди вендоров в среднем и даже более высоком ценовых сегментах. И именно эта персональная уверенность и помогает сэйлам совершать рекорды в продажах. А когда клиент остается довольным, закладывает бренд в «требовательные» проекты и регулярно возвращается за новой партией – чем это не подтверждение высочайших стандартов качества продукции?!
А многие ли задумывались, как же достигается и за счет чего удерживается такое качество? За счет чего оно стабильно от партии к партии? Откуда у нас уверенность, что каждая поставка будет очередным подтверждением истины «NIKOMAX – это качество, превосходящее ожидания», а не игра в рулетку: что в этот раз нам подсунул завод-производитель?
Одно из главных объяснений – мощности, которые были выбраны российской и тайваньской R&D командой. Именно производственные затраты влияют на себестоимость продукции примерно на 90%. Но мы давно осознали, что попытки руководствоваться только соображением низкой себестоимости товара несовместимы с долговременным и стабильным успехом. И потому выбор завода вендором – это или изначальная гарантия качества, или…при ставке на экономию – регулярные выдохи облегчения: «в этой партии обошлось без косяков, гоним дальше». Мы давно проголосовали за первый подход, ему и следуем.
Для того, чтобы своими глазами посмотреть, где и как производится продукция NIKOMAX, я отправилась на Тайвань.
Именно на этом острове расположены штаб-квартиры или представительства многих мировых вендоров, однако далеко не все из них используют локальные заводы для производства. Некоторые тайваньские вендоры регулируют свои издержки и, соответственно, себестоимость конечного продукта, размещаясь на заводах в Китае. Немудрено, ведь как уровень жизни населения, так и стандарты менеджмента и производства на Тайване намного выше. До сих пор надпись Made in Taiwan – это своеобразный (и заслуженный!) знак качества для сетевых компонентов. Команда NIKOMAX ставит качество на первое место, поэтому почти вся продукция, рекомендуемая для использования в гарантийных СКС, производится именно на Тайване.
Так что пристегните ремни и полетели на прекрасный остров, ранее известный как Формоза, а ныне официально называемый Китайской республикой (Republic of China, R.O.C). Мы с коллегами посетим два крупных завода и поведаем вам секреты их качества. Правды ради стоит сказать, что лицезрение представителей Тайле для них не редкость. Регулярные деловые визиты и даже инспекции со стороны разработчика NIKOMAX – это залог двустороннего понимания (и доверия, в конечном итоге!). Да простит меня читающая аудитория за то, что названия самих производственных компаний вынуждены остаться инкогнито в этой статье.
Наша первая точка (назовем ее Завод А) – это семейное предприятие, основанное на Тайване в 1963 году, разросшееся на материковый Китай в 1999-м и ныне суммарно насчитывающее более 700 сотрудников. До конца этого года компания запустит еще одно производственное помещение на острове, площадь которого превзойдет обе имеющиеся территории. Менеджмент Завода А особо подчеркивает низкий уровень текучки кадров, хвастаясь хорошими условиями организации труда для производственного персонала.
Компания специализируется на LAN-кабелях (solid and stranded) и патч-кордах категорий от 5e до 7A конструкций U/UTP, F/UTP, SF/UTP, U/FTP, F/FTP, S/FTP, в том числе готовится анонсировать долгожданную cat. 8. Именно здесь мы производим кабель 9-й серии, который всегда считался флагманом в NIKOMAX, выбирая себе в конкуренты вендоров-лидеров из мировой СКС-индустрии. Не мудрено, ведь все параметры – от конструктивных особенностей до упаковки – сделаны не просто в соответствии с высочайшими стандартами уровня всех «больших имен», но и на одной с ними территории, используя те же машины.
Продукция Завода А сертифицирована UL, ETL and Delta. Используемое оборудование производства Германии, Швейцарии, Великобритании и США потребовало огромных инвестиций, но при этом отбросило менее состоятельных конкурентов назад. Еще одна знаковая особенность – собственная тестовая лаборатория для проверки оболочки кабеля на устойчивость к возгоранию (flame test). В устрашающей на вид камере образцы продукции подвергаются воздействию огня, а разработчики анализируют результаты и добиваются наилучших параметров для основной партии.
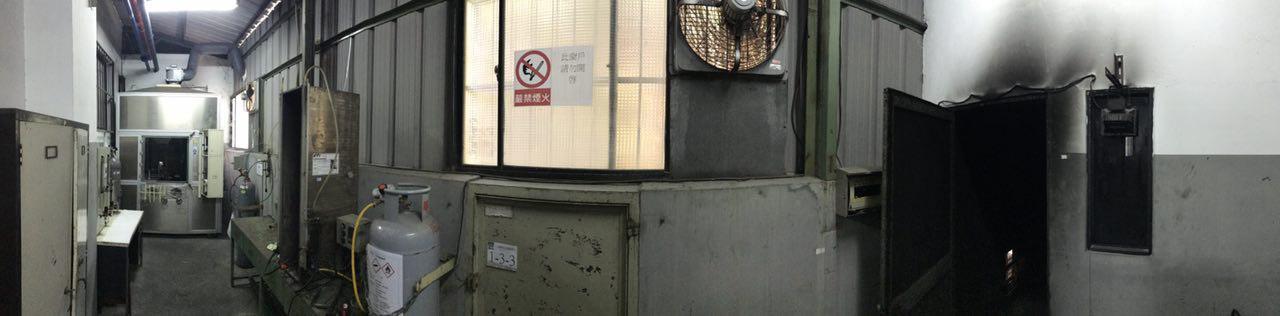
Помимо сетевых кабелей Завод А выпускает USB и HDMI шнурки, а его особая гордость – медицинские кабели, в частности, для эндоскопов и хирургического оборудования. Для их производства пришлось организовать отдельные помещения с особыми требованиями. Например, это изолированная кабина, в которой с работников специальным ветродуем удаляют все пылинки перед тем, как они переступят порог почти стерильного зала.
Руководство Завода А очень строго соблюдает условия non-disclosure agreements, в соответствии с которыми имена всех вендоров, заказы которых занимают производственные линии, хранятся в строгом секрете. Именно поэтому доступ в цеха упаковки и хранения готовой продукции закрыт для всех посетителей. Что же, приходится уважать такую позицию и самостоятельно очертить в голове круг «соседей по конвейеру». С учетом высоты себестоимости кабеля, позволить себе размещаться здесь могут только бренды премиум класса, имена которых, как говорится, «слишком известны, чтобы называть их вслух».
Завод А реализует все этапы производства кабеля, превращая своими мощными машинами огромные мотки меди в готовые бухты. Все начинается с вытягивания медной жилы (copper drawing), в процессе чего толстая проволока утончается до проводника размером 0,50-0,55 мм в зависимости от конструкции и категории кабеля. Будущий многожильный (или «патчкордовый») кабель ждет следующий этап (conductor bunching), на котором 7 проводников объединяются в один пучок.
Затем и стандартный solid, и «патчкордовый» stranded проводники отправляются на процедуру нанесения изоляции (insulation extrusion). Уникальность используемого на заводе оборудования в том, что оно позволяет объединить два процесса. Сначала изоляция наносится на проводник, который затем наматывается на катушку, а следом машина берет изолированные белый и цветной проводники с катушек, свивает воедино и наматывает готовой парой (twist pairing).
По итогам мы видим то, что уже напоминает нам кабель, – большие бобины с двухцветными проводами. Дальше пары могут отправляться на индивидуальное экранирование фольгой для конструкций U/FTP, F/FTP, S/FTP, или же свиваться по несколько (cabling), чтобы стать, к примеру, стандартной «четырехпаркой». А затем сгруппированные пары ждет общая оплетка в виде сетки (braiding) (для S/UTP, S/FTP), фольгирование (для F/UTP, F/FTP) или и то, и другое сразу (для SF/UTP, SF/FTP). Последний этап – нанесение оболочки (jacket extrusion) из приготовленного в собственном цехе PVC или LSZH компаунда.
Вся произведенная продукция проходит многократные тестирования на узкоспециализированных промышленных тестерах, а также с использованием широко известных полевых тестеров Fluke.
Наш второй завод – пусть он будет называться В – проверенный долгими годами работы производитель оконечных компонентов для СКС – коммутационных панелей, модулей keystone, настенных розеток, компонентов для построения оптоволоконных сетей. Основанное в 1983 году предприятие является членом всех ключевых в кабельной индустрии альянсов – TIA, Bicsi, IEEE. Штаб-квартира и основное производство находятся на Тайване, дополнительная сборочная линия в Китае, и еще пара офисов в США.
На Заводе В есть множество линий. Часть из них полностью автоматизированы, например, пайка печатных плат или вставка контактов. Некоторые линии – преимущественно сборка и упаковка – предполагают большое участие ручного труда, а на этапе контроля точность машины и неравнодушие человека объединяются для 100% гарантии качества. Ни один потенциальный недостаток коммутационного модуля не скроется от контролера «3-в-1»: этот аппарат проверяет целостность компонента, соблюдение всех допусков и даже правильность расположения наклейки. Вероятность того, что сначала человеческое око пропустило какую-то проблему, а следом сбой дала автоматика, равен нулю. Именно поэтому коммутационные модули NIKOMAX постоянно участвуют в проектах с 25-летней гарантией – они просто не бывают бракованными.
Мне удалось с замиранием сердца понаблюдать за несколькими процессами с участием наших компонентов. Это готовится очередная партия для России. Вот собираются патч-панели, а с упаковочного конвейера сходят модули и розетки. Готовые пакетики кладутся в транспортные коробки по 150 штук. Я задала вопрос – а как отсчитываются верные количества, как фасовщики достигают точности? Все просто – соответствующий 150 штукам вес показывает прибор, чья погрешность меньше, чем вес одного пакетика. Поэтому, ни 149, ни 151 штук в коробке оказаться не может.
Завод В самостоятельно отливает все пластиковые части панелей, модулей и розеток на основе собственных пресс-форм (molding forms), изготавливаемых в этом же помещении. Эта часть производства является самой дорогостоящей – стоимость одной формы достигает десятков тысяч долларов США. Компания таким образом контролирует и качество используемого пластика, и вид/функциональность готового компонента.
Большинство заводов-конкурентов покупает готовые пресс-формы, т.е. начинает своё производство уже не с самого первого этапа, и таким образом имеет зависимость от третьих сторон в случае поломок.
В отличии от завода А, компания В не только не скрывает, но и очень даже гордится своими клиентами. В тех цехах, которые наиболее связаны с готовой продукцией, можно легко встретить всевозможного размера коробки, пестрящие логотипами очень известных брендов. Какие-то из них почти никогда не конкурируют с NIKOMAX в России – они изначально позиционируются как premium и имеют соответствующее ценообразование. Мы все их знаем, уважаем и даже равняемся – многие из них фактически создавали СКС-индустрию десятки лет назад. Какие-то европейские бренды были для меня неизвестными еще в прошлом году, но с появлением дистрибуторов в Венгрии и Германии NIKOMAX вышел на эти рынки...и обрел новых конкурентов. Сильных. Но лишь на них и нужно ориентироваться.
Мой самолёт в Москву опередит морской контейнер, поезд или фуру не меньше, чем на полтора месяца. Мы встретимся с этими компонентами на складе только осенью. А тем временем наши партнёры-интеграторы уже прописывают их в проекты и согласуют спецификации с заказчиками. Каждый созданный на Тайване компонент выполнит своё предназначение – безотказно служить. За вечно не распишемся, но как минимум 25 лет – гарантированно.
Автор - Белоусова Марина
Заместитель директора по продажам компании Тайле